Abrasion resistant steel plate is made by alloying ingredients such as carbon (C) and iron (Fe) using a range of trace or low level minerals being added to alter the chemical-mechanical properties of the final product.
Initially raw iron is melted in a blast furnace and then carbon is added. Whether or not additional elements such as nickel or silicon are added is dependent on the area of application. The level of carbon present in abrasion resistant steel plate is usually between 0.18-0.30%, characterizing them as low-to-medium carbon steels.
When this reaches the desired composition, it is formed and cut into plates. Abrasion resistant steel plates are not suited to tempering and quenching because heat treatment can reduce the material’s strength and wear-resistance.
Common materials include: NM360 Wear Resistant Steel Plate,NM400 Wear Resistant Steel Plate,NM450 Wear Resistant Steel Plate,NM500 Wear Resistant Steel Plate.
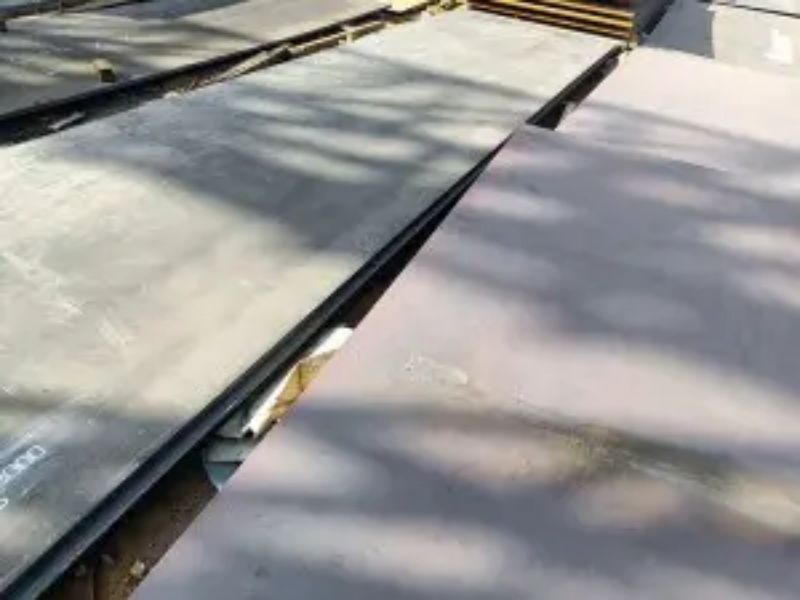
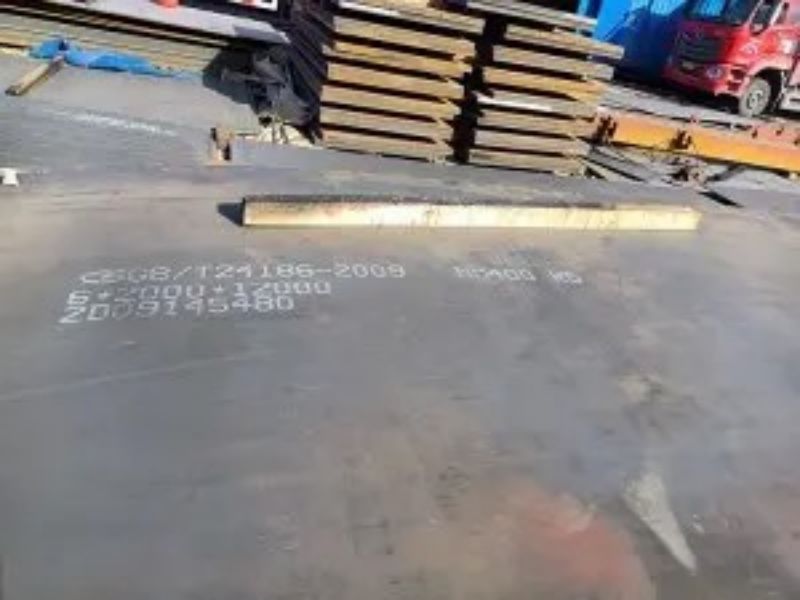
Abrasion resistant steel plate is extremely hard and strong. Hardness is a crucial attribute of abrasion-resistant steel plate, however high hardness steels are often more brittle. Abrasion resistant steel plate also needs to be strong and so a careful balance must be struck. To do this, the alloy’s chemical composition must be strictly controlled.
Some of the applications abrasion resistant steel plate is used in are:
Mining industry machinery
Industrial hoppers, funnels and feeders
Platform structures
Heavy wear platforms
Earth moving machinery
Abrasion-resistant steel plate comes in a range of varieties which all have an exact hardness value on the Brinell scale. Other varieties of steel are graded by toughness and tensile strength however hardness is critical to stop the impact of abrasion.
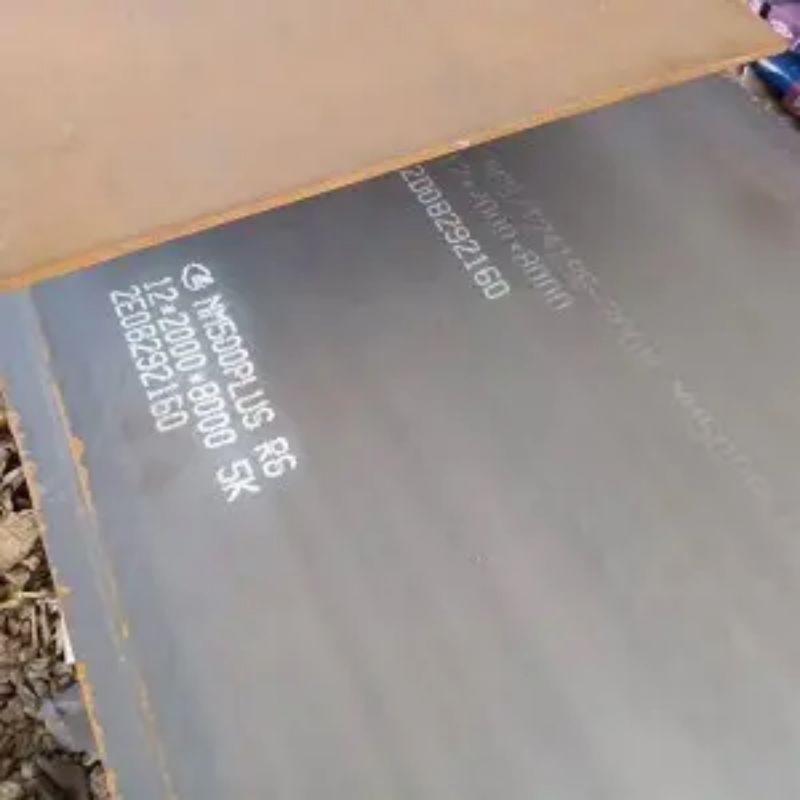
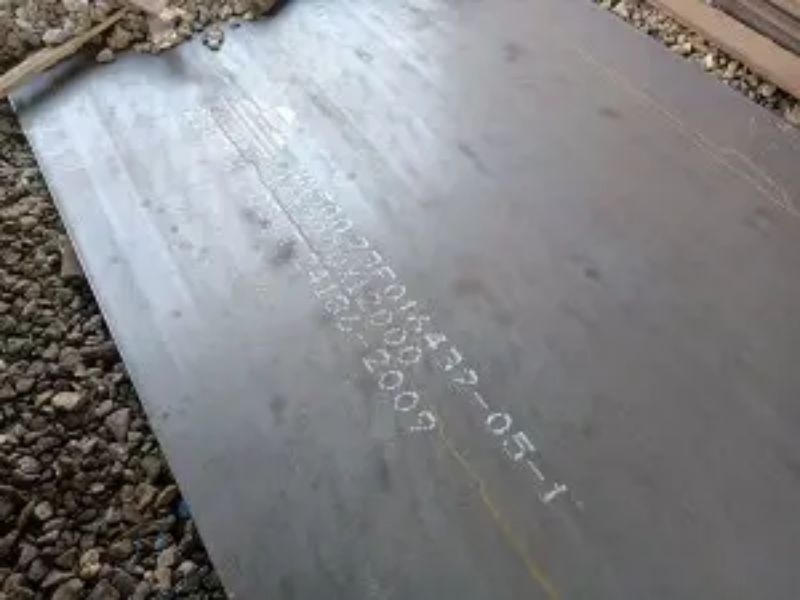
Post time: Apr-07-2024